Any business or organization which is successful in increasing the sales turnover and improving bottom line, uses some tools and techniques to ensure success every time. The methodologies include proper planning, execution and monitoring. The planning process is very similar to that which is available in Automotive Core Tools released by AIAG (Automotive Industry Action Group). The core tools used in this process are APQP (advanced product quality planning), FMEA (failure mode and effect analysis) and PPAP (production part approval process) guidelines.
These core tools are based on Plan-Do-Check-Act methodology and have a structure to ensure effectiveness by covering all relevant aspects.
Ford Motor, General Motor and Chrysler had taken efforts in consolidating the thoughts on using these quality core tools, releasing in the form of guidelines and continuing improvements in these guidelines.
APQP, PPAP, FMEA are the tools for planning a new product or a process with an objective of –
- Reduction in defects (as compared with similar earlier product)
- Timely introduction / launch as required by customer
- Effective (and efficient) utilization of resources (such as money, men)
Generally, the use of these tools is in order of having first APQP plan, use FMEA for making robust product and process design, complete all stages necessary for PPAP and then launch the new product as per agreed delivery terms with customer.
APQP guideline provides the micro level inputs for planning at different stages of a new product development including process development, verification, validation and continual improvement.
APQP focuses on meeting customer requirements at every stage of product realization process including packaging and delivery and establishing control over process through use of appropriate statistical methods.
PPAP is a subset of APQP with addition of few system requirements (like sample products, master sample, etc) to maintain proper records, in case, if customer wants to review at a latter stage.
FMEA guideline provides structure for identifying the potential failures, analyzing the potential causes and helps in prioritizing the actions for preventing failures. FMEA exercise is done at system, subsystem and component levels.
FMEA can also be used to verify robustness of product design and manufacturing processes to manufacture the product that meets customer requirement.
There are other tools such as SPC (statistical process control), MSA (measurement system analysis) which also help in monitoring the process capabilities and ensuring improvement in measurement methods.
These tools, if used with their intent and purpose, can really be helpful in not only achieving ‘Timely Defect Free Product’ but takes us beyond to achieve ‘Right First Time, Every Time’.
Many of non-automobile organizations are using similar approaches under different names such as project planning, quality planning, product / process approval, etc.
The observation is that the sequence of using these tools is somewhat peculiar and almost is as follows -
- Define opportunities
- Identify the potential failures and their causes, obtain solutions (use of FMEA approach)
- Determine various options to overcome the problems
- Plan the implementation of solutions (now the APQP starts)
- Provide approvals and resources
- Plan the project reviews and monitor implementation
Such an approach helps in anticipating the obstacles and overcoming those through preventive actions.
ISO 9001:2015 and other ISO standards also require organizations to adopt risk-based approach. These tools support in documenting and monitoring the issues resulting into risks and opportunities.
Use of the quality core tools in planning seems to be very simple at its face value. Some of the automobile organizations are using these tools. Purposes could be different such as only for certification or for using with its intent and purpose.
Success of using these tools depends upon –
- Having multi-disciplinary team with competent members
- Commitment from top management to review the team recommendations and support for implementation
- Systematic recording of all failure modes and causes through brainstorming session
- Evaluation of different alternatives with proper justifications / data
How TUV India can help organizations to apply these tools effectively?
It is necessary to understand the use of supporting tools in using the quality core tools. For example, one needs to use cause-effect diagram while identifying the causes of potential failures. Also identifying only one cause to fill the format is not adequate, the causes related to man, material, machine, method and environment need to be identified. In absence of use of support tools the right and detailed information may be missing and conclusions drawn would be misleading.
TUV India helps organizations to strengthen the use of these core tools through system audits as per IATF 16949:2016 with ISO 9001:2015. Auditors auditing these standards are well trained and experienced in using these tools. Auditors summarize the strengths and weaknesses to the organization during and after the audit.
TUV India also conducts open house training on these core tools which includes exercises and case studies too. The training duration of 3 - 4 days ensures sharing of experiences, exercises and case studies with coverage of all core tools listed above. Training also includes linkage of these tools to the requirements mentioned in IATF 16949 standard. Training on each of core tool also are conducted with duration of one day wherein the tutor presents the concept, shares practical experience, gives exercises / case studies, reviews the group tasks and resolves queries of participants.
About The Author
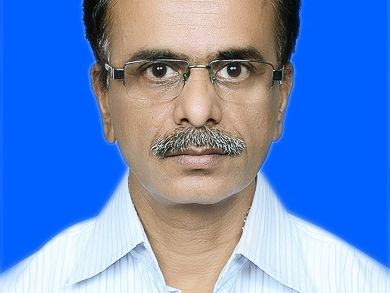
TUV India Pvt Ltd
TUV NORD GROUP
certificationindia@tuv-nord.com